Standard Operating Procedures (SOPs) are structured guidelines for the goals and processes of an organization that provide reliable and integrated information about the most effective strategy for day-to-day business operations. Managers and employees are constantly connected digitally to the network to provide real-time communication and exchange of ideas to improve the SOP. In my experience, the most effective SOPs are performed in collaboration between operators and support teams such as continuous improvement specialists, maintenance technicians, and process engineers. When operators are actively involved, they will invest in the success of SOPs and will strive to adopt them as the new standard for production work.
Without proper management and regular updates, standard operating procedures and work instructions can quickly become outdated and prevent employees from meeting their operational KPIs. Whether you’re trying to sell the world’s hottest sourdough bread loaves or recycle 5,000 tons of non-ferrous metals every day, SOPs help busy teams consistently meet customer demand and run business with minimal error. Basically, standard operating procedures are essential for managing business processes because they provide well-defined ways to accomplish important tasks on a regular basis.
Operation Management
The most effective managers develop standard operating procedures for daily tasks to avoid confusion, increase efficiency, train new employees, and protect everyone. The operations management system enables companies to effectively manage their daily business practices to achieve the highest level of efficiency. The operation management system keeps production and order fulfillment running efficiently, freeing up time to do more useful work.
Operations management improves your external and internal processes, allowing you to better serve your customers while increasing the sales of your products. By improving the business process, the operations manager can stimulate manufacturing innovation that will increase customer satisfaction through better customer service. Implementing operations management to streamline processes can help you better manage your business behind the scenes so you can better serve your customers. Convenient operations management ensures faster delivery, on-time order processing, quality control, and reliable order fulfillment to ensure that your customers receive products on time and in good condition.
Excellence in operations management means planning and monitoring operations to drive growth, implementing processes to improve efficiency, and continually working to improve. Your goal is to optimize your operations management for scalability to help your business reach its maximum potential.
You can improve your business from the top down with the management methodology you follow. When you focus on operations management, you evaluate the business operations and production processes that need to be performed and simplify them without changing your business goals.
If your business is struggling, you might need to simplify your operations and management. When there’s a lack of operational management, companies find it difficult to provide on-time delivery, accurate products, and even good customer service. This is why it’s important to optimize business operations management procedures to improve the efficiency of chief operating officers (COO) and managers in all aspects, including quality control, supply chain management, and workflow.
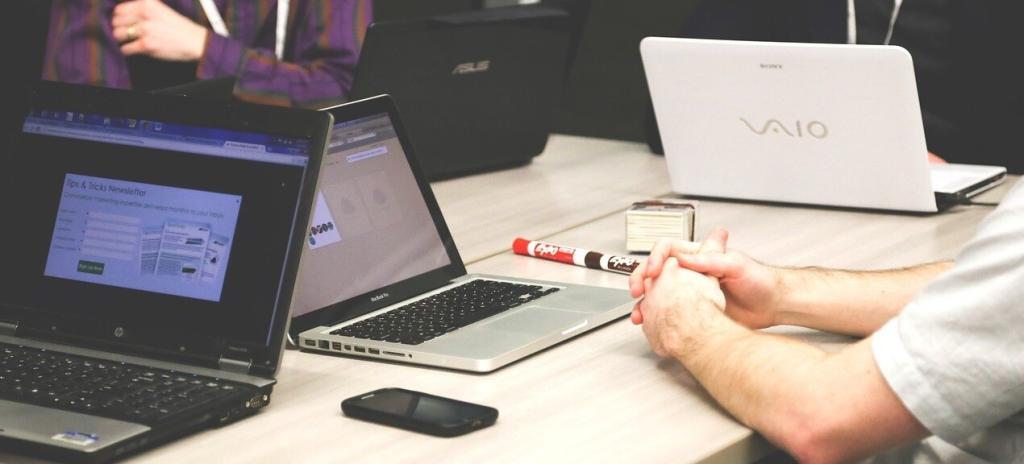
Focus on Results
With a robust Operations Management System (OMS), organizations can build a business structure that points the way to greater productivity and better quality control at a lower cost. Having the right operations management software can help you streamline your business process and manage your production/distribution process effectively. Not only that, it can improve your process and eliminate work bottlenecks by automating repetitive tasks. Good operations management software must be able to collect data and provide you with data-driven reports that enable your team to make the right business decisions.
One way you can do this is by posting your SOPs and training instructions to an online portal that gives workers instant access to the same procedure whenever they need it. Make sure you link any issues to the work standard so that the SOP influences your actual operations. Be sure you test the SOP with other operators on other shifts to ensure that you are indeed choosing the best standard method.
To obtain the best results, management should continuously review SOPs to ensure that they are accurate in the existing working environment, quality control standards, and regulatory requirements. As the name suggests, the step-by-step SOP describes the process step by step in a linear fashion. They are most useful when the operation or process is simple and straightforward enough.
Operations form the backbone of any business, ensuring the smooth operation of processes, delivery of goods, and the receipt of services by customers. Operationally excellent companies operate with the goal of delivering their product or service to the customer at the exact time they want it, at the lowest cost, with the least effort, and at the price, the customer wants to pay. Operational excellence is a structure that enables companies to focus on growth and execute their strategy better than their competitors. Standard operating procedures (SOPs) software in the form of document control and management, change control, and employee training not only ensures compliance but also helps companies achieve their goals faster, saving money.
Final Thoughts
Most small businesses still use periodic inventory management because it does not require complex software or inventory scanning. The system uses store and asset management software to calculate inventory based on sales and purchases.
Putting in place proper inventory management procedures can help ensure that the business is operating at its optimal financial level and that the products meet the needs and expectations of customers. According to David Pike, co-author of Inventory and Manufacturing in Supply Chains, which is now in its fourth year, and professor of supply chain and operations management at the University of San Diego, “Aspiring small business owners will be surprised to see how much help they can get, and the money they can save by managing their inventory wisely. Some simple inventory management software systems can scale to more complex functions as your business grows.
Of course, there is no one-to-one way to organize procedural documentation – SOP checklists, hierarchical lists, and process workflows are common. The table below shows everything that a company could solve using these methods. Operations management also ensures that the company complies with all labor and environmental regulations with an efficient manufacturing process, which means using optimal results with the lowest cost (such as time, energy, and resources).
Also Read: